La simulation de production pour visualiser les process
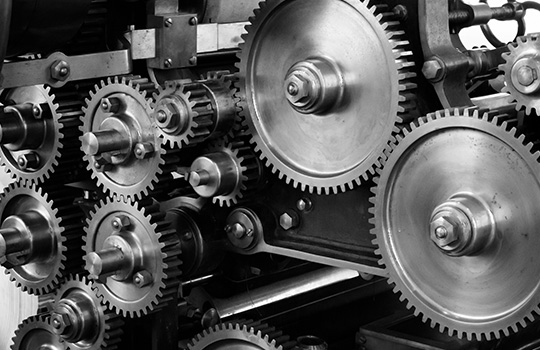
LE SECTEUR de l’industrie :
La production manufacturière française a fortement accéléré en 2017 : + 2,8 %, après + 0,3 % en 2016.
L’activité, portée par un contexte conjoncturel favorable, a progressé dans la plupart des branches.
L’investissement aurait progressé de 3 % en valeur en 2017. Cette année-là, environ 29 % des investissements dans l’industrie manufacturière étaient motivés par le renouvellement de l’outil productif. Les autres principales motivations économiques des investissements étaient la modernisation et la rationalisation des équipements (23 %), l’extension des capacités de production (16 %) ou l’introduction de nouveaux produits (12 %).
LES SOLUTIONS SIMCORE :
La simulation aide les entreprises à améliorer leurs procédés de fabrication.
Les logiciels de simulation permettent de simuler les processus de production complet, (capacités de stockage, planning des opérateurs, taux d’utilisation des équipements) vous permettant d’identifier facilement et éliminer les limitations du systèmes (goulot d’étranglement, besoins en ressources (machines ou humaines)…).
Amélioration des process – Pourquoi la simulation?
- Visualisation et élimination des goulets d’étranglements,
- Augmenter l’efficience et améliorer la qualité,
- Optimiser l’utilisation des ressources,
- Dimensionner les besoins pour une croissance future.
Comment la simulation peut vous aider :
La mise en oeuvre du lean manufacturing via la simulation
Les principaux résultats mesurés par les entreprises :
- Les réductions de coûts de plus de 80%
- Augmentation du débit de 40-80%
- Augmentation de la productivité de 70-125%
- Réduire les travaux en cours de plus de 80%
Utiliser la simulation pour la mise en place d’une procédure six sigma
L’idée centrale de Six Sigma est que si vous pouvez mesurer où les «défauts» (tout ce qui conduit à l’insatisfaction des clients) se produisent dans un processus, vous pouvez systématiquement comprendre comment les éliminer à travers un processus d’amélioration continue et vous rapprocher du «zéro défaut».
Six Sigma est divisé en deux méthodologies DMAIC et DFSS.
DMAIC (Définir, Mesurer, Analyser, Améliorer, Contrôler) se concentre sur l’amélioration des processus et de la performance existants.
Alors que Design for Six Sigma (DFSS) met l’accent sur la génération de nouveaux procédés, produits et services pour répondre aux besoins des clients (CTQ) au niveau Six Sigma.
La rigueur statistique disponible à travers les logiciels de simulation est un complément idéal à l’une de ces méthodes.
Par exemple, la simulation permet aux utilisateurs de comparer les défauts dans un processus d’analyse Six Sigma, et même de prédire les tolérances six sigma.
Pour mesurer la satisfaction du client, la simulation est capable de mesurer des indicateurs de satisfaction financiers, opérationnels et du client dans une même analyse.
Line Balancing et Takt Time
Lors de la conception et de la gestion d’un modèle mixte ligne-montage, les ingénieurs système s’efforcent de satisfaire des objectifs tels que maximiser le débit de la ligne, en minimisant le nombre de stations, le maintien d’un équilibre entre le travail dans les stations, la satisfaction des tarifs de distribution, l’évolution de la gamme de produits, et plus encore.
Avec autant de besoins différents, et potentiellement contradictoires, sur le système, les résultats d’une nouvelle conception de processus, ou re-conception, peuvent être difficiles à prévoir. Les interdépendances entre les contraintes du procédé et les objectifs de conception sont généralement complexes et difficiles à reconnaître. La conception d’un nouveau système ou la re-conception d’une ligne d’assemblage existante incorrecte peut entraîner une perte de production et des surcharges de travail pour les opérateurs.
Les facteurs suivants ajoutent de la complexité à la conception d’une ligne d’assemblage :
- La fiabilité des équipements
- La disponibilité des opérateurs
- La taille des tampons de ligne
- La séquence et la composition des produits
- Les taux d’approvisionnement (bord de ligne) et les volumes
Les méthodes analytiques peuvent être utilisées, mais sont limitées en raison de la nature dynamique du système.
L’impact de la gestion des tampons, les durées des shifts, et le séquencement des produits limitent rapidement cette approche pour la conception de la ligne et son équilibrage.
Pourquoi la Simulation?
La Simulation fournit la plateforme idéale pour tester des conceptions de ligne dans un environnement rapide et sans risque.
Une simple simulation des opérations d’assemblage en ligne vous permet d’identifier les goulots d’étranglement du système, d’exécuter différents plans de production, et d’évaluer l’impact de la conception et de la planification des décisions, telles que les besoins en tampons et les impacts du mix produit.
Cette « what-if » analyse peut être faite rapidement et efficacement, afin d’évaluer tous les critères de décision contradictoires.
La Simulation permet aux développeurs et chefs de ligne d’analyser rapidement le système dans diverses conditions d’exploitation. La simulation est pratiquement une nécessité pour effectuer une analyse rigoureuse et significative sur une ligne de production moderne. Elle est capable de modéliser en fonction du niveau de détail requis et elle peut établir des intervalles de confiance autour de résultats pour un large éventail de questions.
Un exemple : Dimensionnement des tampons entre les machines d’une ligne de production pour NTN
Le contexte
Leader mondial dans l’industrie du roulement, NTN – SNR équipe en roulement les 10 véhicules les plus vendus en Europe et en Asie.
L’objectif de la simulation est de dimensionner les convoyeurs entre les machines de 2 lignes de production de pièces usinées.
Les résultats
Les différentes phases de ce projet ont permis d’aider NTN à décider des technologies à mettre en œuvre sur les différentes machines de ses lignes de production. L’étude a notamment mis en avant un gain de productivité de 6 % avec l’utilisation d’outils spécifiques sur certaines machines des lignes.
La phase 2 a mis également en avant l’importance de la priorisation des pannes, qui permet un gain de productivité de l’ordre de 1%. L’impact de cette priorisation est la chose importante que NTN souhaitait démontrer auprès des techniciens qui interviennent sur ces pannes. Des phases supplémentaires du projet sont dédiées à cette sensibilisation auprès des opérateurs.
Les références
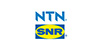
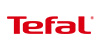
Tefal
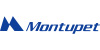
Montupet
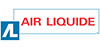
Air Liquide
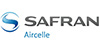
Aircelle
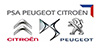
PSA