Les avantages d’une Simulation de flux Process avec SIMUL8
- Créez des simulations rapidement avec des fonctionnalités puissantes et de la flexibilité
- Simulez n’importe quel processus et expérimentez des changements dans un environnement sans risque et sans coût additionnel.
- De l’analyse stratégique de haut niveau aux conceptions opérationnelles, créez rapidement des simulations en utilisant l’interface de glisser-déposer intuitive de SIMUL8 et utilisez le langage de codage Visual Logic pour une personnalisation avancée.
- Avec le moteur de simulation le plus rapide disponible sur le marché, vous pouvez passer moins de temps à construire des simulations et plus de temps à expérimenter pour obtenir les réponses dont vous avez besoin pour prendre des décisions.
Vos besoins ?
- Votre système n’atteint pas les performances attendues,
- Vous avez besoin d’optimiser votre outil de production pour réduire vos coûts,
- Vous avez besoin de mesurer la réponse de votre outil industriel à de nouveaux marchés ou à de nouvelles contraintes,
- Vous souhaitez automatiser vos lignes de production ou entrepôts,
- Nous vous proposons une étude de flux dynamique à l’aide d’un logiciel expert.
- Nous mettons à votre disposition notre expérience dans la simulation de flux pour valider et optimiser vos systèmes industriels et logistiques.
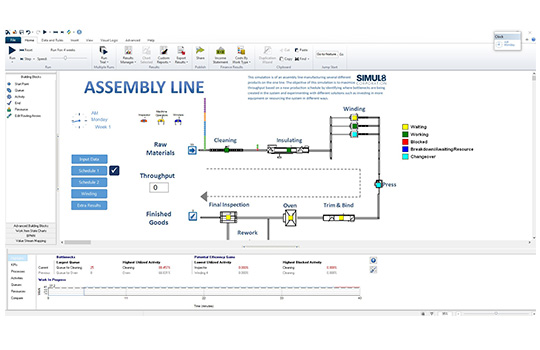
Notre méthode
Nos consultants connaissent votre secteur d’activité et votre métier. Pour faciliter vos prises de décisions ils s’appuient sur la simulation des flux physiques, des implantations, et l’organisation humaine correspondante.
La méthodologie utilisée lors du projet de simulation est la suivante :
- Définition des objectifs durant la réunion de démarrage,
- Rédaction de la spécification technique et des données,
- Collecte et vérification des informations,
- Définition du scénario,
- Modélisation par nos consultants expert,
- Validation avec votre équipe,
- Expérimentation,
- Fourniture du rapport et d’un film de la simulation.
Vous avez une question sur l'utilisation de la Simulation de flux Process avec SIMUL8 ?
Contactez-nousL’exploitation du modèle de simulation
Expérimentation et analyse :
- Lancement des scénarii en faisant varier les paramètres
- Multiplicité des runs avec voies aléatoires différentes -> tester la sensibilité du système
- Analyse des résultats notamment par rapport aux indicateurs critiques définis avec le client
- Possibilité d’ajouter des résultats complémentaires pour affiner l’analyse.
Optimisation :
- Durant l’expérimentation des améliorations seront mise en place (si besoin) en concertation avec le client.
- Après chaque optimisation les runs sont a relancer pour mesurer l’impact.
Réunions de travail en utilisant le modèle pour répondre aux questions et tester des configurations ou règles différentes
LES PLUS DE NOTRE PRESTATION
- 25 ans d’expérience,
- Réalisation de nombreux projets,
- Utilisation d’outils Experts reconnus par tous les fournisseurs de systèmes automatisés,
- Utilisation des caractéristiques mécaniques de vos équipements,
- Une équipe à votre service.
Questions Fréquentes
Quelques questions (et réponses) pour mieux appréhender SIMUL8.
Quels sont mes goulots d’étranglement ?
Définition : Un goulot d’étranglement est un point d’un système limitant les performances globales d’un flux de production d’une entreprise.
Dans un système de production ou un système logistique il est important d’identifier les points goulots, soit (si c’est possible) pour les éliminer, soit (si ce n’est pas possible) pour s’assurer que ce process soit toujours alimenté pour qu’il soit toujours au maximum de sa capacité.
Par exemple pour une ligne de production, pour une machine goulot on s’assurera d’avoir du travail en attente devant cette machine pour que le désamorçage ne vienne pas pénaliser en plus la production de la machine.
Dans ce cas d’étude, nous avons simuler une ligne d’usinage connectée pour la société NTN.
Cette ligne est constituée d’un ensemble de machine différente, avec des contraintes de temps de cycle, de temps de changement d’outillage, de temps de maintenance…
En fonction du mix produit, de la taille des lots, … nous avons pu détecter que la machine goulot était une machine de tournage.
A cette étape nous avons lancer une campagne de scénario en modifiant la capacité des tampons inter machine, afin de les dimensionner au plus juste. Nous avons ainsi prévu un stock de sécurité en amont des machines goulots pour qu’elles aient toujours du travail en attente.
Dans une première phase d’amélioration, NTN nous a demandé de tester différentes technologies d’outillages pour améliorer la production de ces machines. La solution retenue était plus coûteuse que celle initialement choisie, mais a permis une augmentation de production de l’ordre de 6%.
Dans une seconde phase d’amélioration, NTN nous a demandé d’éprouver les stratégies opérateurs sur les interventions lors de panne. Les lignes de production étant sujettes à de nombreux arrêts, le but de cette phase était de mesurer l’impact sur les productions globales des différentes stratégies pour intervenir sur les pannes. Le scénario 1 simulait le comportement du système dans le cas où les opérateurs ne changent pas de missions une fois choisie. Le scénario 2 ajoutait une importance aux missions et autorisait les opérateurs à stopper la tâche en cours pour intervenir sur une mission plus importante.
La conclusion de cette phase 2 est que la priorisation des pannes permet de gagner en productivité de 1%, notamment en intervenant plus rapidement sur les machines goulot.
Conclusion :
Les différentes phases de ce projet ont permis d’aider NTN à décider des technologies à mettre en œuvre sur les différentes machines de ses lignes de production. L’étude a notamment mis en avant un gain de productivité de 6 % avec l’utilisation d’outils spécifiques sur certaines machines des lignes.
La phase 2 a mis également en avant l’importance de la priorisation des pannes, qui permet un gain de productivité de l’ordre de 1%. L’impact de cette priorisation est la chose importante que NTN souhaitait démontrer auprès des techniciens qui interviennent sur ces pannes. Des phases supplémentaires du projet sont dédiées à cette sensibilisation auprès des opérateurs.
Comment dimensionner mes équipements avec la simulation ?
Dans la construction d’un projet, la définition du besoin « fonctionnel » est une première étape. Comment et avec quoi produire?
Une fois cette question résolue, vous devez ensuite déterminer :
- Le type de machine (différentes solutions technologiques, fournisseurs…)
- La capacité des stocks et autres tampons,
- La façon de répondre aux contraintes de production (mix produit, …)
- …
Une approche statique (calcul dans un tableur), vous permet d’approcher les besoins moyens de vos équipements. Mais comment est-ce que cela va vivre dans le temps :
- lorsqu’il y aura des arrêts (pannes, maintenance, changement de réglage,..),
- en fonction des volumes demandés,
- en fonction des plannings des opérateurs
- …
Pour répondre à ces questions vous avez besoin de passer par une approche dynamique : la simulation de flux.
L’article suivant vous présente comment utiliser le logiciel SIMUL8 pour répondre à ces questions :
Comment mesurer l'impact des aléas sur ma production ?
Une machine qui ne produit pas, c’est au final de l’argent perdu.
La maintenance, notamment préventive, est un point délicat car il s’agit d’arrêter sciemment une machine pour éviter qu’elle ne tombe en panne plus tard.
Pour justifier des budgets (opérateurs et matériel) il est bon de pouvoir quantifier l’impact des différents arrêts.
10 pannes de 1 minutes n’ont pas le même effet qu’une panne de 10 minutes.
La première étape est de bien connaitre les différents indicateurs et leur signification (voir l’article : TRS et autres TAUX ).
Ensuite nous vous proposons une suite d’articles sur l’impact des pannes :
L’impact de la typologie des arrêts sur l’efficience (Part1).
L’impact de la typologie des arrêts sur l’efficience (Part2).
Pour augmenter la production, faut-il ajouter une nouvelle machine ?
Simcore réalise de nombreuses études de dimensionnement pour des ateliers de production. Le contexte est souvent le même, une augmentation de besoin de production et des questionnements sur la capacité de production des équipements. Dans de nombreux cas l’ajout de matériel est pressenti, mais le client sollicite une étude pour confirmations.
Dans 80% des cas une meilleure utilisation des équipements existants, éventuellement l’ajout d’opérateur suffit à couvrir le besoin.
L’article suivant est un exemple illustrant le fait que gagner en production est souvent lié à une amélioration de l’utilisation des outils déjà à disposition :
Pour augmenter la production, faut-il ajouter une nouvelle machine ?
Découvrez l'ensemble de nos services et compétences adapté(e)s à votre secteur d’activité (Diagnostic de performance, Simulation de flux, Optimisation des chargements...
nos services et compétences