Avant Propos :
Dans le secteur Automobile, l’amélioration et l’optimisation des processus est un travail constant. Depuis de nombreuses années, la simulation de flux est utilisé pour optimiser la conception des lignes d’assemblages.
Les simulations peuvent fournir un banc d’essai rapide et sans risque pour la conception et la mise en œuvre de votre installation de fabrication.
Ce cas d’étude montre comment cela peut être réalisé en utilisant SIMUL8.
Sommaire :
- Contexte et Objectif
- 1- Modélisation dans le logiciel SIMUL8
- 2- Comprendre le process
- 3- Analyse de la simulation
- 4- Analyse des résultats
- 5- Prendre les bonnes décisions
Contexte et Objectif :
Lors de la conception d’un atelier de Ferrage automobile flexible et efficace, les objectifs sont de répondre aux problématiques suivantes :
- Stratégie de vitesse de ligne (survitesse et pousser ou tirer)
- Stratégie de gestion des buffers
- Optimiser les boucles de transport
- Détermination des emplacements des buffers de sous-composants
- Analyser le film de production et les impacts de la séquence
- Batch Build vs Build-to-Schedule
- Manutention de matériaux et ressources partagées (chariots élévateurs et main-d’œuvre)
Tous ces objectifs contiennent des facteurs interdépendants qui rendent difficile de tester les décisions de manière indépendante et de prévoir l’impact global sur la ligne.
La simulation permet d’intégrer des événements aléatoires, tels que les pannes de machines. C’est donc un outil analytique puissant et robuste qui donne de la visibilité sur les performances de votre installation, avant la mise en œuvre.
C’est pourquoi l’industrie automobile s’est appuyée pendant des décennies sur la simulation pour mener à bien les lancements de programmes de véhicules.
1- Modélisation dans le logiciel SIMUL8
La première étape est de transformer notre problématique en un modèle de simulation. Le logiciel Simul8 rend cette étape très rapide et facile.
De l’optimisation des Luges* à la programmation de l’ordonnancement, nous vous expliquons les étapes les plus importantes de la conception et de la mise en œuvre de votre installation automobile à l’aide de la simulation.
* : Une Luge est la plate-forme qui maintient le véhicule en place pendant qu’il se déplace dans l’installation
2- Comprendre le process
Il existe généralement 3 installations associées à la fabrication d’une automobile : atelier de carrosserie (Ferrage), peinture et opérations finales.
L’atelier de Ferrage est l’endroit où l’on assemble les tôles pour former la caisse du véhicule. Une fois la caisse assemblée, elle est ensuite envoyée à l’atelier de peinture.
Ensuite, le véhicule peint se dirige vers le montage.
L’industrie automobile utilise depuis longtemps la simulation dans ses usines et ses services d’exploitation de véhicules pour modéliser ces process et les optimiser.
Jetons un coup d’œil à un atelier de Ferrage générique et explorons comment la simulation est utilisée pour optimiser les futurs programmes fabrication des véhicules.
La puissance de la simulation permet de modéliser un l’ensemble des processus d’une usine de fabrication.
Comme vous pouvez le voir sur le modèle de simulation, un atelier de Ferrage typique contient plusieurs lignes séquentielles et de nombreux points de rendez-vous clés où les sous-composants doivent être soudés ensemble.
3- Analyse de la simulation
Un avantage important de l’utilisation de la simulation est la possibilité d’effectuer une analyse de scénario « What-If », comme le test de divers ordonnancements.
Dans cette simulation, il existe 3 types de véhicules différents, où les commandes arrivent avec un profil de probabilité de 50 %, 35 % et 15 % (voir Figure 1).
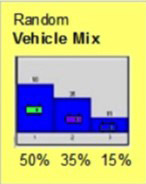
Souvent, différents types de véhicules peuvent nécessiter un type de Luge unique, ce qui complique le planning de production. S’assurer qu’il y aura une Luge vide disponible lors d’un appel à partir du calendrier de production peut être difficile à concevoir.
Le planning de production n’est pas seulement important pour les commandes des clients, mais aussi pour garantir que les positions d’assemblage clés auront le bon sous-composant à temps.
Dans cet exemple, il y a 3 zones principales où la séquence peut sortir de l’ordre d’origine (représentées par Seq. A, Seq. B et Seq. C).
Cela est généralement causé par des lignes parallèles, des buffers, des tests de qualité ou des boucles de reprise.
Le maintien de la séquence peut être critique à divers points du système, en particulier lors du lancement de l’ordre de fabrication des sous-composants.
C’est le cas pour un ensemble côté véhicule, comme le montre cette simulation, car il peut y avoir 3 styles uniques par type de véhicule.
Les études de simulation aident à la définition du meilleur algorithme pour la mise en œuvre de schémas « Build to Schedule » ou « Batch Build ». Cette simulation envoie un ordre de fabrication à la zone d’assemblage des côtés du véhicule sur la ligne 3 pour coordonner la production (voir Figure 2).
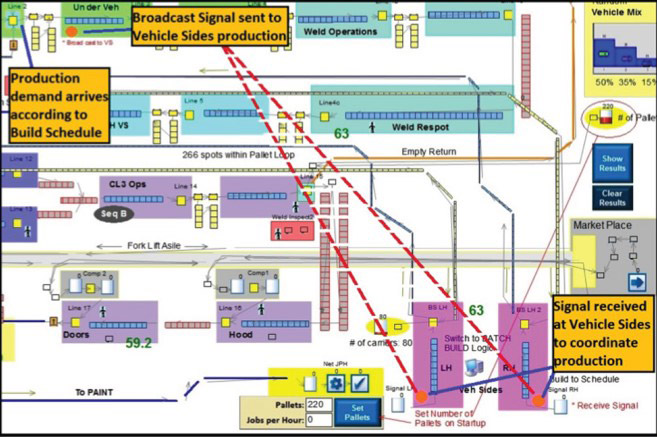
4- Analyse des résultats
Habituellement, plus le lancement est précoce, plus il a de risque qu’un « hors séquence » se produise.
Tandis que le lancement au plus proche du point d’assemblage (fabrication « juste à temps ») augmente le risque de perte de performances potentielles due aux attentes.
La réalisation d’une analyse de simulation approfondie est essentielle pour développer un système robuste et flexible ; qui peut gérer plusieurs types de véhicules.
Optimisation des supports
Dans notre simulation, nous avons 220 Luges dans la « boucle de transport » et 266 emplacements maximum dans le système lorsqu’il se déplace dans la boucle.
Habituellement, nous commençons l’opération avec une Luge vide.
Pour rendre les choses plus compliquées, nous pourrions produire plusieurs types de véhicules voyageant tous sur les lignes flexibles.
Les « boucles de transport » ont besoin d’espace pour s’étendre et se contracter afin d’assurer un débit optimal ; les retards dus aux temps d’arrêt ou aux changements peuvent dégrader les performances.
Nous devons nous assurer qu’une luge vide est disponible et prêt pour la prochaine opération, sans toutefois bloquer une machine de transfert.
La simulation est la meilleure solution pour visualiser vos boucles de transport et l’ensemble de leurs interconnexions.
Alors maintenant que votre simulation est prête pour la phase de test, il est temps d’utiliser vos résultats pour vous fournir une conception basée sur les données pour votre usine de fabrication.
Ceci est particulièrement critique lorsqu’il s’agit d’investissement en capital : le coût des Luges et des transporteurs s’additionne rapidement et le calcul des niveaux corrects est vital pour les marges bénéficiaires d’une organisation.
Regardons un exemple de notre simulation, nous sommes en mesure de modifier le nombre de Luges disponibles pour la boucle principale. Cela nous permet de déterminer une plage de fonctionnement fiable pour le nombre de transporteurs au sein du système ; trop peu peuvent entraîner de longs retards et un trop grand nombre peut provoquer des blocages indésirables.
À l’aide du bouton intégré « Définir les palettes », nous pouvons personnaliser les entrées de simulation et commencer à tester différentes valeurs. Après avoir effectué cela pour des valeurs par incréments de 10 de 100 à 260, le tableau et le graphique suivants ont été construits (voir les figures 3 et 4).
- En bleu: l’estimation sans simulation
- De vert à rouge: les valeurs de moins en moins acceptable
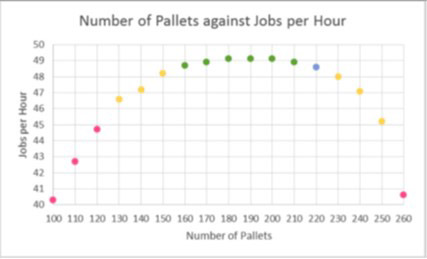
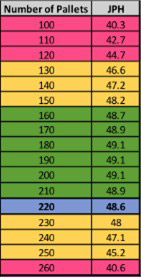
Ces résultats montrent comment, à partir d’un nombre de support de départ de 220, il est possible de réduire le nombre de Luges utilisées à 160 sans subir une diminution de la production horaire (Job Per Hour). En réalité, on observe d’abord une augmentation de la productivité, la diminution du nombre de luge a fluidifié le process.
5- Prendre les bonnes décisions
Maintenant que nous avons nos résultats, nous pouvons maintenant aider la direction à prendre les bonnes décisions.
Une seule Luge avec tout son équipement de contrôle peut coûter jusqu’à 25 000 €, et une usine peut avoir 250 Luges dans son système.
Si la décision était prise que le Job Per Hour actuel était satisfaisant, à 25 000 € par Luge, ce changement de conception permettrait à l’organisation d’économiser 1 500 000 € – un capital qui serait libéré pour investir ailleurs dans l’entreprise.
Ce n’est qu’un exemple de la façon dont nous pouvons utiliser la simulation pour concevoir une installation automobile et fournir des résultats étayés par des données qui peuvent aider à la prise de décision de gestion.