La simulation de flux : un levier efficace de performance pour l’entreprise
Les réponses apportées par la simulation de flux sont transverses. Quelques soient les secteurs d’activités, depuis l’agro-alimentaire jusqu’au nucléaire par exemple, on retrouve globalement les mêmes problématiques. Les différences observées sont principalement d’ordre environnemental. Les échelles de temps constituent un autre facteur différenciant d’un métier à l’autre.
Mais dans tous les cas, le même besoin fondamental est exprimé : obtenir de la visibilité pour mieux comprendre les interactions entre tous les éléments d’un environnement de production ou de logistique, dans le but de prendre la meilleure décision. Cette décision résulte le plus souvent d’un arbitrage directement issu des études de simulations : il s’agira, à partir des différents scénarii testés, du plus optimiste au plus pessimiste, de trouver le meilleur compromis possible pour l’entreprise considérée.
La stabilité du système est une condition indispensable pour garantir la qualité du service et de l’installation au client final.
Sommaire
- La phase de conception du projet : estimer le besoin
- Retour d’expérience de la simulation de flux
- La phase de validation du cahier des charges : qualification et dimensionnement du besoin
- La phase d’expérimentation : la modélisation d’une usine virtuelle
- Les gains liés à la simulation de flux
La phase de conception du projet : estimer le besoin
Lors de la phase de conception du projet, il est nécessaire de poser tous les éléments chiffrés qui constituent ou impactent la problématique de flux à traiter. Les premières estimations ainsi réalisées permettront de dimensionner le besoin.
Dans cette phase, le meilleur outil reste Microsoft Excel. Outil de bureautique « simple » et largement répandu, il a le gros avantage de faciliter le partage des informations entre les parties prenantes à la définition du projet.
On peut alors choisir soit d’utiliser des données existantes (du site considéré ou d’un autre site industriel connu), soit de faire des projections.
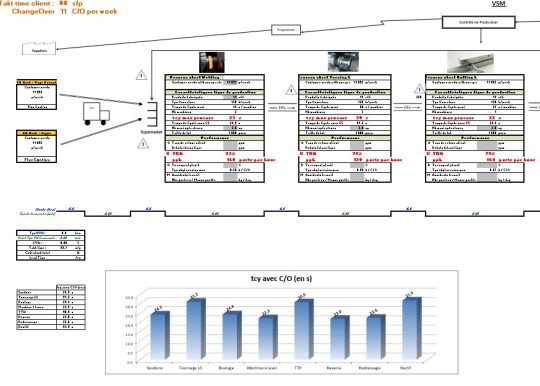
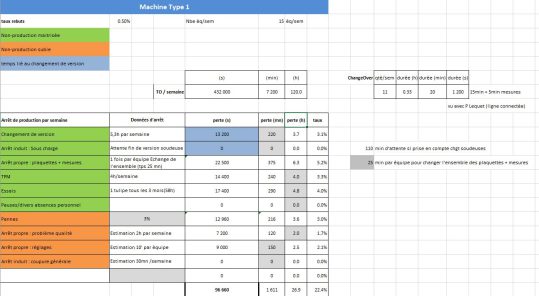
Les multiples fonctions d’Excel (formules, macros, code VBA…) permettent de faire un grand nombre de calculs en intégrant de multiples critères (conditions, répartitions…). On peut ainsi calculer la variation d’un flux en intégrant des variables telles que la disponibilité d’une machine ou l’impact d’une panne.
Avec Excel, les calculs réalisés dans la phase de définition et de conception du projet permettent d’obtenir une bonne vision du besoin : la définition des paramètres sur lesquels on va pouvoir influer s’en trouve précisée. Les données collectées pourront et devront être utilisées pour la suite du projet.
Mais il y a plusieurs limites à cet exercice :
- Un calcul statique sans prise en compte de l’échelle de temps > illustration : la performance d’un procédé peut être avérée selon un critère « volume » mais ne plus répondre au besoin si on se place du point de vue du temps de réalisation, trop long.
- Pour chaque calcul, un résultat en fonction des valeurs unitaires des paramètres > illustration : augmenter le nombre d’AGV (chariots automatiques) a des limites liées par exemple à l’espace disponible et aux conflits potentiels de circulation (image du trafic routier).
- Chaque calcul prend en compte une seule configuration, empêchant une vision globale si on travaille sur plusieurs flux (production, logistique…), sans possibilité de croiser > illustration : ajouter une machine peut compenser un besoin, mais il faut prendre en compte que cette nouvelle machine va potentiellement perturber les autres.
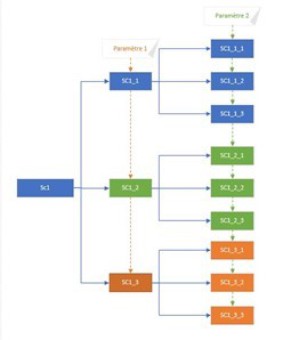
Retour d’expérience de la simulation de flux
L’objectif du projet était de dimensionner la taille d’un stockage temporaire en fonction d’un flux continu de produits entrants qui devait ensuite être traité par un process de cuisson discontinu.
Le calcul Excel est réalisable avec un seul flux entrant et un seul flux sortant. Cela devient impossible lorsqu’il faut effectuer l’analyse avec plusieurs flux entrants (lignes de production) et de multiples flux de sortie en parallèle (appareils de cuissons). Le nombre de variables à prendre en compte voue à l’échec toute tentative de calcul.
Dans un calcul classique sous Excel, pour simplifier le modèle, il faut travailler avec des données moyennes : cadences théoriques, TRS, ouverture des lignes… Mais la réalité n’étant jamais si figée, les calculs ainsi générés seront éloignés de la situation réelle. Par exemple, les pauses et les temps de chargement des opérations discontinues créent des temps de non-fonctionnement durant lesquels les produits s’accumulent.
Seule la simulation peut faire apparaître ces détails car le calcul est dynamique. Les pics apparaissent clairement. En fonction de leurs fréquences et valeurs, il est alors possible d’adapter l’organisation afin de les limiter pour ne pas construire un stockage trop grand. Le dimensionnement est fait au plus juste.
Autre avantage de la simulation, c’est sa capacité d’itération. Une fois le modèle établi, il est aisé de le faire fonctionner plusieurs fois avec un jeu de paramètres différents. Les comparaisons entre les différentes situations sont donc facilitées.
Benoît BARSACQ – Responsable Amélioration Continue, Sécurité et Environnement (Société MARIE Groupe LDC)
La phase de validation du cahier des charges : qualification et dimensionnement du besoin
La simulation dynamique conceptuelle avec SIMUL8 (ou analyse fonctionnelle)
Après analyse de tous les flux de façon indépendante, il vient alors le temps d’utiliser la simulation pour y introduire :
- La notion d’évolution dans le temps
- Les diverses interactions (entre les flux, les machines…)
- La variabilité (la dimension aléatoire impacte grandement l’enchaînement des éléments et il faut donc pouvoir balayer un maximum de configurations pour s’assurer de la stabilité du système et de la qualité des résultats)
A cette étape de la réflexion du projet, on ne possède pas encore d’implantation des éléments. Les modèles de machine ne sont pas non plus définis. Seule la capacité attendue du futur système est connue. Dans ces conditions, on peut utiliser un outil de simulation dynamique, dit conceptuel. Il s’agit d’un logiciel permettant de générer une simulation depuis un simple diagramme de flux.
SIMUL8 répond à ce besoin en proposant un logiciel de simulation pour visualiser et expérimenter des processus et prendre des décisions en toute confiance :
- Expérimentation et analyse :
- Lancement des scénarii en faisant varier les paramètres.
- Multiplicité des runs avec voies aléatoires différentes pour tester la sensibilité du système.
- Analyse des résultats, notamment par rapport aux indicateurs critiques définis avec le client.
- Possibilité d’ajouter des résultats complémentaires pour affiner l’analyse.
- Optimisation
- Mise en place de facteurs d’amélioration, si besoin, durant l’expérimentation et en concertation avec le client.
- Relance des runs après chaque optimisation pour en mesurer l’impact.
Pendant ce processus, des réunions de travail permettent, en utilisant le modèle, de répondre aux questions des parties prenantes au projet et de tester des configurations ou des règles différentes.
Une fois cette étape finalisée, le besoin est alors qualifié et dimensionné : la phase d’expérimentation peut débuter.
La phase d’expérimentation : la modélisation d’une usine virtuelle
La simulation dynamique détaillée
Avec des systèmes intégrant de l’automatisation, l’analyse fonctionnelle devient insuffisante. En complément indispensable, il faut également s’assurer que l’ensemble des éléments est en capacité d’assurer la livraison des produits dans les temps. Dans une simulation dynamique conceptuelle, un déplacement est représenté par un temps (calculé en amont). Mais dans un système faisant intervenir par exemple des AGV, un véhicule pourra avoir besoin d’un temps de parcours différent en fonction du trafic sur l’installation. Pour intégrer ce type de contrainte, il faut alors utiliser une simulation dynamique détaillée (et non plus conceptuelle) avec un logiciel tel qu’AUTOMOD.
Le logiciel de simulation 3-D AUTOMOD permet de modéliser la conception des installations et de simuler des systèmes logistiques, de manutention ou de distribution :
- Prise en compte de l’implantation physique (plan à l’échelle)
- Mise en place de la transitique
- Mise en place des Flux / Process
- Mise en place des logiques de pilotage
- Mise en place des résultats :
- L’engagement des équipements,
- L’accumulation sur les équipements,
- Le suivi des stocks,
- Les cadences horaires effectivement réalisées.
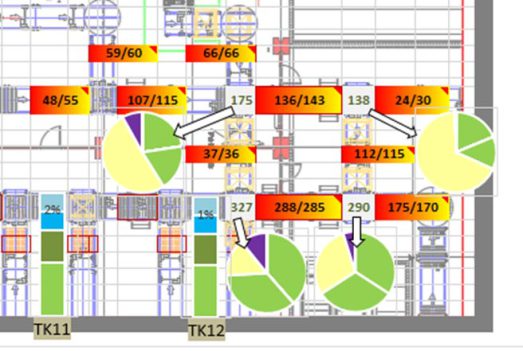
A l’issue de la réalisation de l’expérimentation et de la phase d’optimisation, on obtient une représentation qui s’apparente à une usine virtuelle de la future installation.
Une fois le cahier des charges mis à jour avec ces différents éléments, on aura alors l’assurance que le système fourni correspondra au besoin, pour l’immédiat comme pour le moyen terme.
Les gains liés à la simulation de flux
Un outil puissant d’analyse des systèmes complexes
Comme on vient de le démontrer, la performance globale d’un système de production est le résultat d’une interaction complexe de nombreux facteurs qui, superposés, nécessitent une représentation modélisée du système industriel. La cohérence de ses multiples composantes les unes par rapport aux autres en dépend.
La simulation est l’un des plus puissants outils d’analyse des systèmes complexes. Aujourd’hui, elle est devenue indispensable pour résoudre les problèmes d’optimisation des flux physiques ou des flux d’informations dans les systèmes de production manufacturiers.
Parmi les gains induits, on retiendra notamment :
- Sur les implantations : lors du développement de la simulation, des améliorations sont faites avant le lancement de la construction (gains sur le génie civil et sur les équipements).
- Sur l’informatique (règles de pilotage).
- Sur la mise en service et la phase de démarrage
- Sur la capacité d’anticipation et de mesure des impacts sur les changements de mode de fonctionnement.
La réduction, voire l’élimination du doute lors de la prise de décision, améliore indéniablement la performance des entreprises et optimise leur efficacité. La réduction des coûts est également clairement induite par ce processus de simulation de flux.