Case study: simulation in the factory SENOBLE
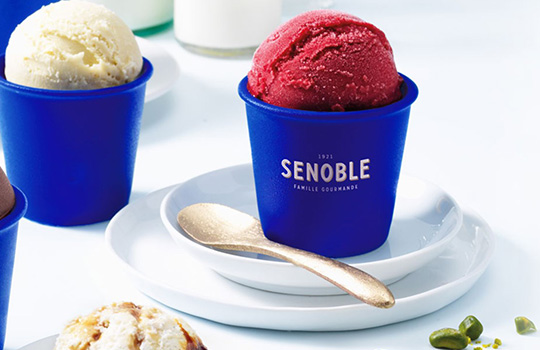
Objective of the study
The objective of the study is to dimension an automated storage system for SENOBLE.
Description of the studied system
10 TK with 10 levels (24 alveolus of 3 palettes), meaning 14,400 places
2 entry-exit levels:
Lower level:
• Entries from the reception;
• Exits of allotment;
• Exits of complete palettes;
• Picking exits (particular mode);
Lower level:
• Exits of complete palettes;
• Picking exits.
Description of the study
For each scenario, it should be noted to measure:
• The distance travelled by the TKs and per TK;
• Flow evolution curves per 15 minute-steps and per level (picking, allotment, complete palette, total per level);
• Duration of a journey between storage exit (after the deposit of the TK by the conveyer) and destination (the picking spot of the conveyer): average time, minimum, maximum and standard deviation;
• Comparative tables between the demands and the realisations.
In order to establish a meticulous model of the system, the storage-destocking algorithm has been integrated.
The benefits of the study
An optimisation research of stock entry-exit management according to the capacity has been led during the study as well as the optimisation of level management for the stock exits.
In order to improve the transportation system, a priority management of the TK exit conveyers has been put in place.
This study has allowed dimensioning and optimising the implantation of the automatic stock before its installation.