Simulation software
Flow simulation helps decision making by quantifying current performance and evaluating the implementation of new solutions.
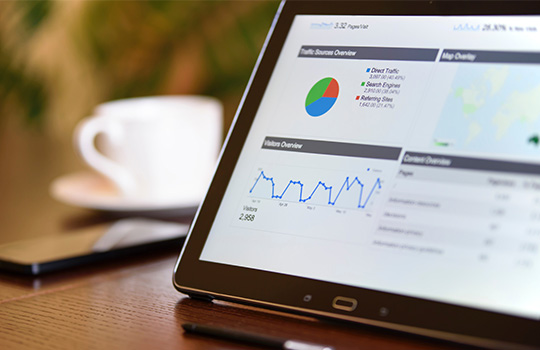
what is a simulation software?
We use a model when we want to understand a real system that we cannot observe or experiment directly, because the system does not exist yet or because it is hard to manipulate.
Then, it is possible to measure the relative impact of each of these components on the global performance of the production system with a simulation. Thus, the establishment of a model and the simulation of the operative part of the system allow providing with necessary information for the control system.
The establishment of a model is the conception process of a system’s model, whereas the simulation is an installation process of the model and the simulations done based on that model. The aim is to understand the behaviour of the system and/or evaluate different strategies for different operations of the system.
Simulation is one of the most powerful analysis tools of complicated systems. Today, it has become essential to solve optimisation problems of physical or information flows in a manufacturing production system.
Objectives of the simulation:
Simulation allows evaluating the performances of a data configuration system:
- In the physical structure (conception of new systems);
- In the decision system (exploitation, reorganisation).
Simulation allows answering the question “what would we get if we did this?” but does not answer the question “what do we have to do to get this?”
To get to an interesting solution, we have to test a sufficient number of scenarios in order to compare them and keep the most interesting ones.
Therefore, simulation is an approach by induction (particular case study in order to get to a conclusion, the most general possible) and not by deduction (solutions obtained by a reasoning, an algorithm.)
In production, simulation allows evaluating the following effects:
- Abolition/addition of machines/workforces;
- Alteration of the manufacturing process: range, manufacturing and preparation time;
- Presence of manufacturing risks: machine breakdown, inventory shortages, urgent orders;
- Stocks’ capacity;
- Authorisation: policy of launch, management rules of waiting lines, resource appropriation;
- Addition of new products/abolition of existing products.
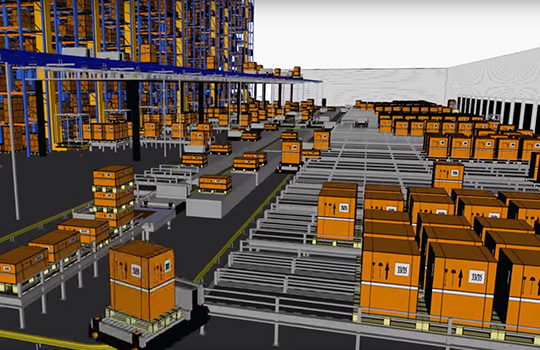
Flow Simulation study
Our consultants are able to perform flow simulation studies using the following flow simulation software:
- AutoMod,
- Simul8,
- Flexsim,
- Enterprise Dynamics,
- ExtendSIM,
- Witness,
- Simio,
- Arena,
- Quest,
- Others to consult us